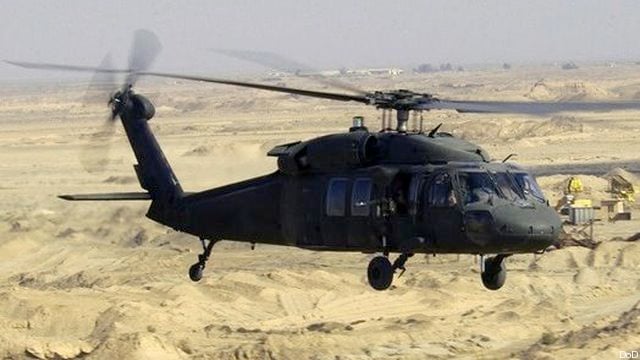
UH-60L Black Hawk over Iraq
WASHINGTON: Wichita State University in Kansas is taking an Army Black Hawk helicopter apart piece by piece, scanning each component to create a detailed three-dimensional model that could be be used for 3D printing, the head of Aviation & Missile Command told reporters this afternoon.
“We have a UH-60 Lima [that] we are currently disassembling,” AMCOM chief Maj. Gen. Todd Royar explained. “[For each] component, they’re scanning it, making a 3D model of it, putting it in a CAD [Computer-Aided Design] file… We’ll start to get those back in a couple of months.”
Just how many different components are there in the UH-60L model of the Black Hawk?
“We expect to probably get about 20,000 structural parts, -ish, out of that,” Royar said. “We’ll take a look at it and evaluate every one” to see whether it can be safely and economically replaced with a 3D-printed version.
Other branches of Army Materiel Command are conducting even more massive efforts. Tank-Automotive Command (TACOM), which sustains and maintains ground vehicles is assessing about 48,000 parts for their suitability to be 3D-printed. Communications-Electronics Command (CECOM) is assessing roughly 98,000.
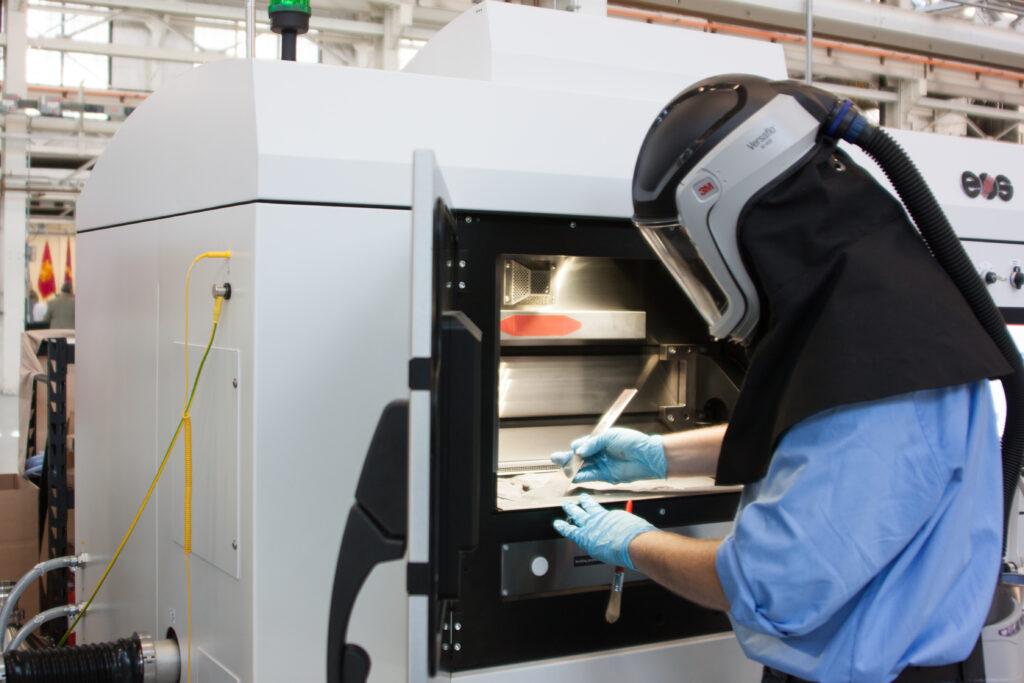
A worker checks on 3D-printed parts at Rock Island Arsenal, Ill.
CECOM is not quite one-third of the way through, said its commander, Maj. Gen. Mitchell Kilgo. So far, he said, they’ve evaluated 31 percent of the parts – over 30,000 items – and found 252 that are “potential candidates for additive manufacturing.” That’s less than one percent.
Why is this so hard? 3D printers can be made simple enough for schoolkids to use. But if you’re trying to print a part that’ll hold up in battle or in flight, you can’t just eyeball the original and guesstimate the dimensions to enter into the printer. Even a detailed blueprint might not include enough detail to turn the 2D drawing into a 3D model accurate enough for printing.
Now, companies that use modern digital design techniques produce 3D models of their new parts as a matter of course, and they often share these with the government. TACOM has such data files for the new Infantry Squad Vehicle, for instance, and plans to 3D print some parts as a proof of concept. But digital models simply don’t exist for vast inventories of older parts, some dating back decades.
To make a model where none exists, you need to use a specialized scanner – some are handheld, others mounted on robotic arms – to map each part in three dimensions, creating a CAD file.
That’s just one step in a complex process, explained Brig. Gen. Darren Werner, commander of TACOM, which oversees the Army’s new Advanced Manufacturing Center of Excellence at Rock Island Arsenal.
You have to study and analyze parts to identify which might be suitable for 3D printing, because not everything is. For example, some components might come under so much stress that they’re best machined from a single, solid block of metal, using traditional “subtractive” manufacturing, instead of additive manufacturing that builds objects up layer by printed layer. They might need to be made of special materials, or specially treated, in ways that 3D printers can’t yet handle. They might be just too big for the available printers to produce: At Rock Island, Werner said, the largest item they can 3D-print is about the size of a hotel mini-fridge. Other parts might be possible to print but cheaper to make the old-fashioned way – so there’s an economic element of the analysis, not just an engineering one.
Once you’ve identified a suitable part, you need to certify that the 3D-printed version will be safe and reliable. That’s one of the most demanding and time-consuming parts of the process, the generals at today’s press conference agreed, especially for aircraft where components must meet Army and FAA flight-safety standards.
“It’s relatively easy, once you have a 3D model, to print something,” said Royar, who’s the Army’s airworthiness certification authority, “but to ensure that it meets the qualification standards, that’s hard.”
Once you’ve certified the part, you can start 3D printing it in bulk – and doing quality control to ensure each individual copy is up to spec. When you print that specific model in that specific printer, does the output meet all the proper tolerances? Does it do so consistently every time? Does a seemingly slight change, like feeding the printer a different batch of powdered metal, cause a significant difference in the final product?
Only once you’ve answered all these questions satisfactorily can you issue the printed part to maintenance troops, contractors, and Army depots for use with actual military equipment.
Despite all these hurdles, all the armed services, not just the Army, see tremendous potential in 3D printing that makes it worth this effort. The military holds onto equipment for decades, long after the production line has shut down, in many cases after the original manufacturer and their suppliers have gone out of business, so there’s no one out there who can make a particular part: The Army would have to fund someone to recreate the tooling and techniques. In other cases, a part may be absolutely critical to a weapons system working, but only a handful need replacement every year, so the profit margin for industry to make and sell them the traditional way would be too slim.
In the scenario that has military logisticians most excited, a unit in combat, its supply lines under attack or cut off altogether, could potentially 3D-print its own repair parts on demand. Instead of transporting an “iron mountain” of different spares, not knowing which ones the unit will actually need, it could deploy with an archive of 3D models, a few printers, and a supply of powdered feedstock for printing. This kind of battlefield additive manufacturing has the potential to liberate frontline units from long supply lines and make them much more maneuverable in the fast-faced all-domain operations envisioned for future wars.
from Hacker News https://ift.tt/2T1Zjbe
No comments:
Post a Comment
Note: Only a member of this blog may post a comment.